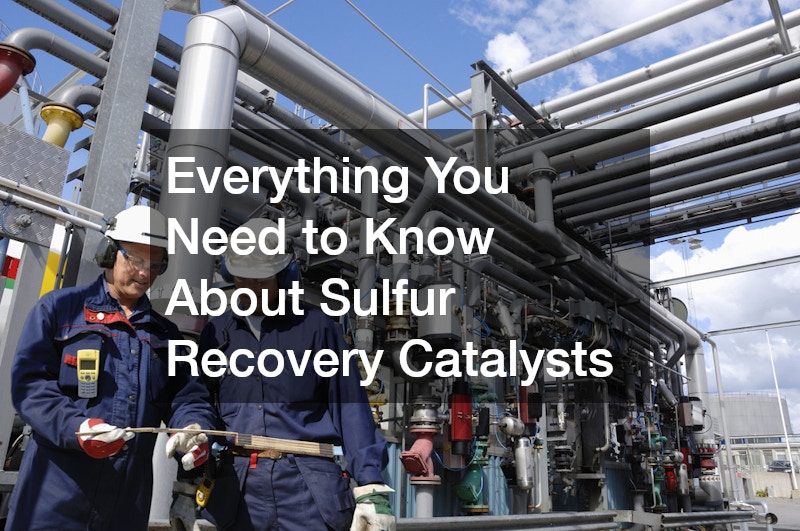
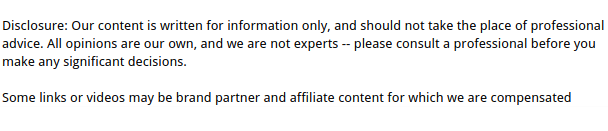
Sulfur recovery catalysts are essential in the process of recovering sulfur from industrial gases, particularly in industries such as petroleum refining and natural gas processing. These catalysts facilitate the conversion of hydrogen sulfide (H2S), a common sulfur-containing compound, into elemental sulfur through a process known as the Claus process. Sulfur recovery catalysts are critical for ensuring the efficiency and effectiveness of this conversion, which helps in reducing the environmental impact of sulfur emissions and improving the overall quality of the industrial output.
The use of sulfur recovery catalysts not only aids in meeting regulatory requirements but also contributes to resource recovery and waste minimization.
The effectiveness of sulfur recovery catalysts depends on several factors, including their composition and operating conditions. Typically, these catalysts contain materials such as alumina, titanium dioxide, or specialized metal oxides, which are designed to enhance the reaction rates of the Claus process. Proper management of operating conditions, such as temperature and pressure, is crucial for maximizing the performance of sulfur recovery catalysts. Additionally, regular maintenance and monitoring are necessary to ensure the catalysts remain effective over time. By understanding and optimizing the role of sulfur recovery catalysts, industries can achieve more efficient sulfur recovery, reduce environmental impact, and ensure compliance with stringent emission regulations.